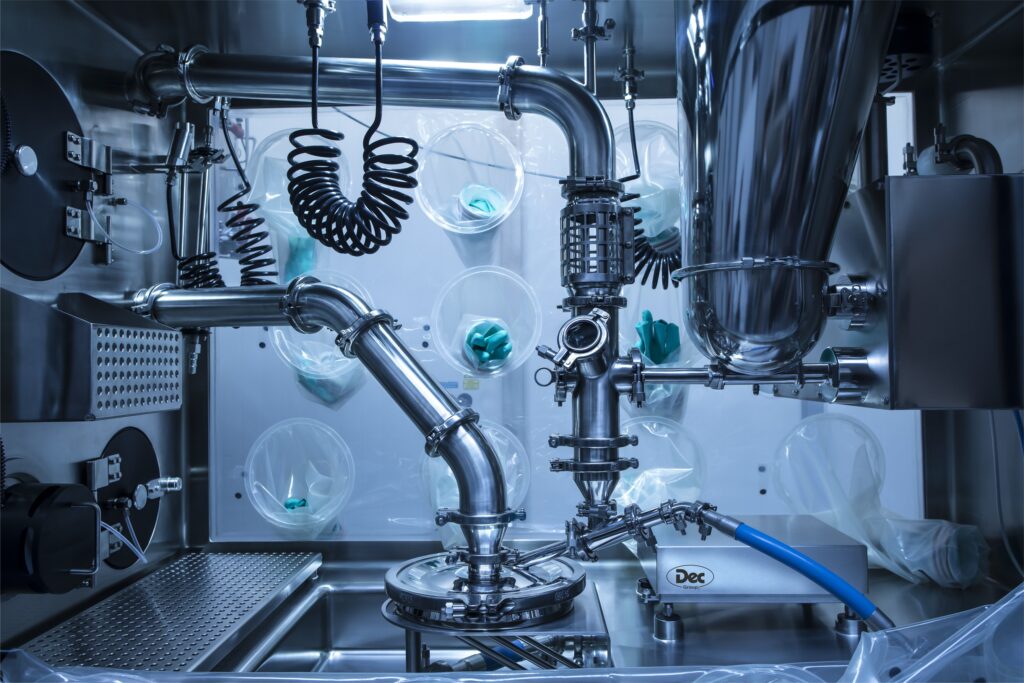
W ostatnich latach nastąpił znaczący wzrost ilości producentów wysoce aktywnych składników farmaceutycznych (HPAPI – Highly Potent Active Pharmaceutical Ingredients) dla rynku leków generycznych. Jest to wynikiem, między… innymi, wygasania patentów, wzrostu ekonomicznego oraz podwyższenia standardów służby zdrowia w rozwijających się Indiach i Chinach.
Wzrost popytu = dynamiczny rozwój
Wraz ze wzrostem popytu, firmy farmaceutyczne będą zmuszone zwiększać swoje inwestycje na rzecz rozwoju produkcji HPAPI. Możemy to osiągnąć poprzez działania stricte wewnątrz organizacji oraz poprzez zakontraktowanie zewnętrznego wykonawcy, co z perspektywy przewidywanych kosztów może okazać się bardziej atrakcyjne. Niezależnie od wyboru, zawsze wymaga to wysokiej klasy wyspecjalizowanych rozwiązań z dziedziny izolacji procesu produkcyjnego.
Określamy rodzaj ochrony na podstawie Limitu Ekspozycji Zawodowej (OEL – Occupational Exposure Limit), po przekroczeniu którego operator zostaje narażony na niebezpieczeństwo.
Idąc dalej, składniki HPAPI zostały pogrupowane w Przedziały Ekspozycji Zawodowej (OEB – Occupational Exposure Band) poziomu 4 (<10µg/m3) oraz 5 (<1µg/m3). Systemy izolacji procesów produkcyjnych dla substancji toksycznych oparte są na wytwarzaniu podciśnienia. Dzięki temu mamy większą pewność, że wszelkie potencjalnie niebezpieczne związki chemiczne pozostaną wewnątrz izolatora.
Limit Ekspozycji Zawodowej (OEL – Occupational Exposure Limit)
Przedział Ekspozycji Zawodowej (OEB – Occupational Exposure Band)
W zależności od poziomu toksyczności danego produktu, jego transfer „z” i „do” izolatora, może odbywać się w bardzo zróżnicowany sposób – począwszy od prostych śluz, po zaawansowane technologicznie rozwiązania typu portów RTP (Rapid Transfer Port). Ujmując rzecz krótko – im wyższy poziom toksyczności, tym bardziej zaawansowane i kompleksowe rozwiązania należy zastosować. Aby zapewnić dalsze zabezpieczenie procesu, powietrze wydostającego się z izolatora należy przefiltrować z użyciem filtrów HEPA (High Efficiency Particulate Absorption), których skuteczność wyłapywania cząstek wynosi ~99.995%. Dzięki temu mamy możliwość zatrzymania niemal wszystkich cząstek produktu w izolatorze, jednocześnie zapewniając odpowiednią wymianę powietrza, zgodnie z obowiązującymi Dobrymi Praktykami Produkcyjnymi (GMP – Good Manufacturing Practices).
„(…) im wyższy poziom toksyczności, tym bardziej zaawansowane i kompleksowe rozwiązania należy zastosować (…)”
W przypadku aplikacji sterylnych, izolatory stają się coraz częściej akceptowanym rozwiązaniem zarówno od strony obowiązujących regulacji, jak i z perspektywy finansowej. Ciśnienie powietrza (bądź innego zastosowanego gazu) jest wyższe niż atmosferyczne, uniemożliwiając przedostawania się zanieczyszczeń do wnętrza izolatora. W tym przypadku użyte zostaną filtry HEPA, bądź ULPA (Ultra-Low Particulate Air [filter]) z opcją użycia laminarnego i/lub turbulentnego przepływu powietrza.
Izolacja procesów sterylno-toksycznych
Projektowanie systemów mających służyć obsłudze produktów jednocześnie sterylnych i toksycznych, wymaga szczególnego zestawu umiejętności oraz wiedzy. Tego rodzaju systemy stanowią kombinację technologii sterujących przepływem powietrza, jak również specjalistycznych systemów obsługi produktu.
Grupa Dec stanowi jedną z bardzo niewielu firm posiadających odpowiedni know how i praktyczne doświadczenie w dziedzinie projektowania oraz produkcji ergonomicznych izolatorów, używanych w badaniach sterylności, w takich gałęziach jak badania i rozwój (R&D), przy rozładunku filtro-suszarek oraz całej gamie innych procesów produkcyjnych, takich jak mieszanie, dozowanie, transfer, również między poszczególnymi izolatorami dzięki opatentowanej technologii Dec PTS.
Mikronizacja
Kolejnym aspektem specjalizacji Grupy Dec jest mikronizacja produktu w warunkach standardowych, izolowanych i sterylnych. Technologia ta umożliwia produkcję bardzo małych cząstek używanych w przemyśle farmaceutycznym, chemicznym oraz kosmetycznym, np. przy produkcji pigmentu, wypełniaczy, czy też produktów wziewnych (inhalatorów). Rozmiar cząstek oraz rozkład wielkości cząstek (PSD) są czynnikami mającymi olbrzymi wpływ na właściwości i charakterystykę produktu. Przykładowo – wpływ zmniejszenia wielkości cząstek na biodostępność jest kluczowym czynnikiem dla wydajności produktu końcowego.
Grupa Dec oferuje kompletne linie skalowalnych młynów – począwszy od małych jednostek przeznaczonych dla działów R&D, po rozwiązania przeznaczone dla skali produkcji przemysłowej – w wielu różnych konfiguracjach i formatach, co umożliwia dostosowanie do różnych wymogów Klientów.
Postęp w dziedzinie redukcji wielkości cząstek
W związku z licznymi zapytaniami od Klientów, Grupa Dec przygotowała nową generację DecJet 30. Nasze młyny rozwijamy z pomocą symulacji CFD, przeznaczonych głównie dla procesów R&D w przemyśle farmaceutycznym. Zoptymalizowana wewnętrzna geometria młynów Grupy Dec umożliwia lepszy przepływ cząstek (Smooth Flow). Dzięki temu mamy możliwość uzyskania węższego rozkładu wielkości cząstek, uzyskując w efekcie bardziej ujednolicony wynik procesu mikronizacji.
Jednocześnie, oferujemy uproszczone wersje dla przemysłu chemicznego, kosmetycznego oraz spożywczego. Ich elementy wewnętrzne wykonujemy ze specjalnie dobranych materiałów, aby dostosować je do wymogów danej branży oraz konkretnej aplikacji. Ponadto Grupa Dec dysponuje centrum testowym, które umożliwia przeprowadzenie prób z produktem Klienta, celem dobrania optymalnego rozwiązania dla danego produktu.
wpis: mikronizacja, HPAPI, izolacja, inertyzacja, farmacja
Home » Aktualności » Uncategorized »